Secondary Steam Reforming Catalyst with High Ni content for Syngas Progress
- Model
- SYAMCAT Z317/SYAMCAT Z318
Item specifics
- Active Components
- Nickel Oxide
- Catalyst Carrier
- Gamma Alumina
- Color of SYAMCAT Z317
- Black grey
- Color of SYAMCAT Z318
- Tile green
- Side crushing strength/(N.granula-1)
- ≥200
Review
Description
Description of Secondary Steam Reforming Catalyst
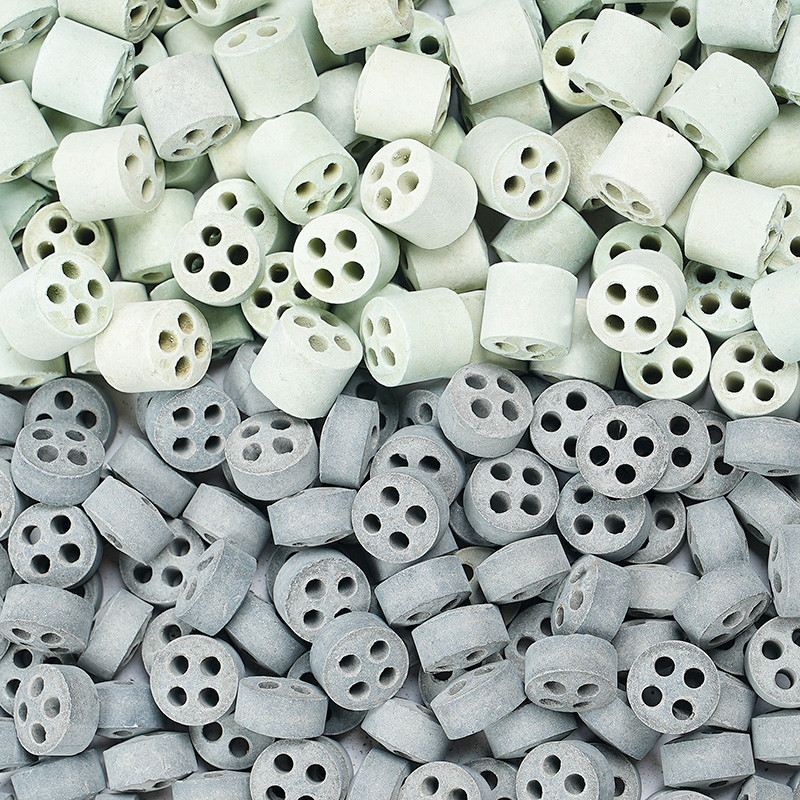
Secondary Steam Reforming Catalyst with High Ni content for Syngas Progress
Optimize your syngas production with SYAMCAT's Secondary Steam Reforming Catalyst, featuring a high nickel content for superior performance. Specifically designed for high-temperature secondary or autothermal furnace steam reforming processes, this catalyst ensures excellent activity, heat resistance, and structural stability.
Application of Secondary Steam Reforming Catalyst
Synthesis Gas Progress: Used in steam reforming process of hydrocarbons to produce hydrogen, ammonia synthesis gas, methanol synthesis gas, oxo- synthesis gas, carbon monoxide etc..
A wide range of feedstock: Suitable for hydrocarbon feedstock, such as light hydrocarbons, refinery off-gas, natural gas etc., which can be used alone or in combination.
Various types of tubular reformers: Suitable for various types of tubular reformers with top-fired, side-fired, bottom- firebox or other configurations such as heat exchanger etc., SYAMCAT Z317 should be loaded in the upper section of the secondary reformer tubes, while SYAMCAT Z318 loaded in the lower part.
Operating Conditions of Secondary Steam Reforming Catalyst
Item
|
Hydrogen
|
Ammonia syngas
|
Methanol syngas |
Oxo-syngas
|
Inlet temperature/℃
|
450-650 |
450-650 |
450-650 |
450-650 |
Outlet temperature/℃
|
700-900
|
650-850
|
800-980 |
800-980
|
Pressure/MPa
|
Atmospheric-6.0
|
Atmospheric-6.0
|
Atmospheric-6.0 |
Atmospheric-6.0
|
Steam/carbon ratio | ≥2.7 | ≥2.7 | ≥2.5 | ≥1.5 |
Carbon space velocity/h-1 | 500-2000 | 500-2000 | 500-2000 | 500-2000 |
Feedstock | Natural gas, oil field associated gas and other gaseous |
Specification of Secondary Steam Reforming Catalyst
Physico-chemical properties
Item
|
SYAMCAT Z317
|
SYAMCAT Z318
|
Shape
|
4-hole cylinder with dome
|
4-hole cylinder with dome
|
Size/mm
|
Φ16*φ4*8~10
|
Φ16*φ4*15~17
|
Active component
|
Ni
|
Ni
|
Bulk density/(kg.L-1) | 0.95-1.10 | 0.90-1.05 |
Benefits of Secondary Steam Reforming Catalyst
Cost-Effective Reforming: Experience unparalleled hydrocarbon steam reforming activity, coupled with outstanding anti-carbon performance and structure stability. Our catalyst ensures efficient processes, reducing your operational costs significantly.
Innovative Design for Efficiency: The unique 4-hole cylinder shape with a dome provides a vast external surface area, higher porosity, and superior gas flow distribution. This design minimizes pressure drop, enhancing efficiency, and reducing energy costs.
Versatile Feeds, Consistent Performance: Adapt seamlessly to various hydrocarbon feedstocks, including light hydrocarbon, refinery gas, or natural gas, either alone or in combination. Switching or adjusting feed dosages doesn't disrupt the catalyst's functionality, ensuring uninterrupted operations.
Effortless Activation, Immediate Production: Our catalyst offers excellent reducibility, enabling direct introduction of natural gas feedstock without extensive pre-activation. This streamlined process saves time, ensuring swift startup and immediate production.
Resilience Against Poisoning: With exceptional anti-poisoning and regeneration properties, our catalyst can self-renew under mild poisoning conditions and undergo in-situ regeneration when severely affected by substances like sulfur or chlorine. This resilience guarantees continuous operations, minimizing downtime and maximizing output.
Flexible Process Integration: Whether your steam reforming process includes pre-reformers or not, our catalyst integrates seamlessly. It accommodates pre-reformer switching on/off cases effortlessly, providing you with the flexibility to adapt your processes based on demand fluctuations and operational requirements.
Adaptable Feedstock Acceptance: Our catalyst boasts high acceptance of feedstock gas and adapts to changes in feedstock gas adjustments, ensuring consistent performance regardless of variations. This adaptability maximizes efficiency and reduces operational uncertainties.
Simplicity in Operation: Experience straightforward reduction processes and user-friendly operation. Our catalyst simplifies complex operations, allowing your team to focus on efficient production without unnecessary complications.
High Nickel Content for High-Speed Operations: Specifically designed for high airspeed conditions, our catalyst features high nickel content. This characteristic ensures optimal performance even in demanding environments, enhancing your production capabilities and operational efficiency.