Enhancing Ammonia Synthesis: A Guide to Safe and Efficient Catalyst Reduction
- Share
- Issue Time
- Jan 3,2024
Summary
The reduction process and adjustments for ammonia synthesis catalysts encompass multiple steps to ensure both safety and efficiency in operation.
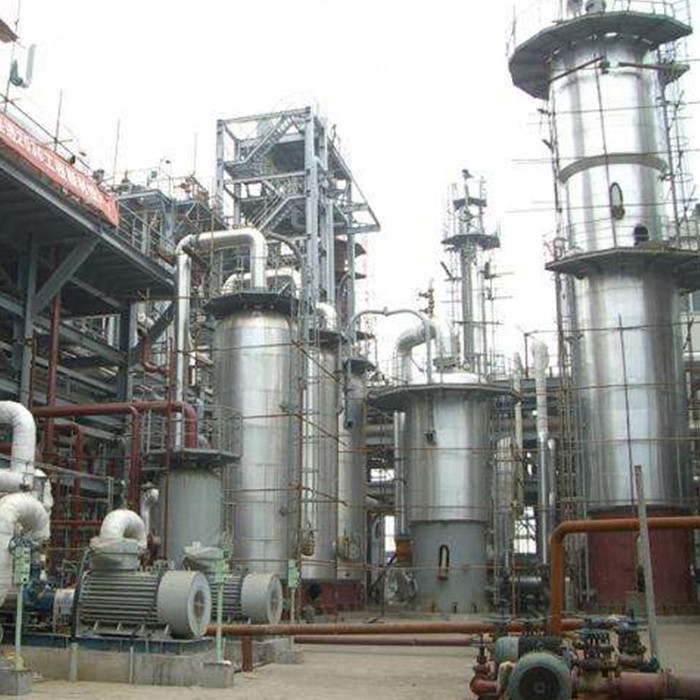
Enhancing Ammonia Synthesis: A Guide to Safe and Efficient Catalyst Reduction
The reduction process and adjustments for ammonia synthesis catalysts encompass multiple steps to ensure both safety and efficiency in operation. Here is an overview of the process:
System Check and Pressurization
After confirming the synthesis loop, the system undergoes pressure testing, displacement (O2<0.5% qualifies), pressurization, and activation of the circulation pump.
Benefit to Customers:
Systematic checks, including pressure testing and displacement, establish a secure operating environment, minimizing risks for customers.

Power Adjustment for Electric Furnace
Gradual increase of electric furnace power to its maximum while ensuring gas safety. For facilities with startup heating furnaces, burner adjustment regulates gas flow to meet temperature requirements.
Benefit to Customers:
Optimized power settings contribute to energy savings and operational cost-effectiveness for customers.
Calculation of Safety Gas Volume
Calculate safety gas volume based on parameters like voltage (U), current (I), gas mixture heat capacity (Cp), temperature difference (t) between the heating wire and gas flow, with a safety factor (C) usually taken as 1.1 to 1.20.
Benefit to Customers:
Precise calculation provides customers with an understanding of gas requirements, contributing to resource efficiency and cost management.

Reduction Reaction and Activation
As the reduction reaction progresses, the catalyst becomes active, accompanied by ammonia synthesis. Heat for the reaction comes from the heater and the exothermic ammonia synthesis. Circulation rate adjustments evenly distribute ammonia synthesis reactions throughout the bed.
Benefit to Customers:
Controlled reduction ensures effective ammonia catalyst activation, leading to improved ammonia synthesis performance and higher production efficiency.
Control of Bed Temperature
Adjust circulation rate to control bed temperature, ensuring a uniform distribution of ammonia synthesis reactions. Avoid unnecessary pressurization unless needed to meet temperature requirements.
Benefit to Customers:
Temperature control contributes to consistent and optimal reaction conditions, positively impacting product quality and yield.

Increased Airspeed for Lowering Water Vapor Concentration
Increasing airspeed reduces system water vapor concentration, especially during the main reduction phase. Careful adjustments avoid excessive pressure while maintaining the desired bed temperature.
Benefit to Customers:
Improved process conditions reduce potential issues related to water vapor, enhancing overall synthesis process efficiency.
Monitoring and Conclusion of Reduction
Regular monitoring of bottom bed temperature, system water vapor, and circulation rate determines whether reduction should continue. Different catalysts may have varied temperature indicators.
Benefit to Customers:
Real-time insights enable informed decision-making for proactive management and maintenance.

Environmental and Operational Efficiency
Optimization minimizes waste and ensures controlled gas release, enhancing environmental efficiency. Operational efficiency is improved, reducing downtime and increasing overall plant productivity.
Benefit to Customers:
Enhanced environmental and operational efficiency contribute to sustainable and productive ammonia synthesis.
In summary, these steps collectively contribute to operational safety, energy efficiency, catalyst performance, and overall process optimization, providing customers with a reliable and efficient platform for ammonia synthesis.
The above briefly introduces “Enhancing Ammonia Synthesis: A Guide to Safe and Efficient Catalyst Reduction” , If you would like to learn more or are in search of a manufacturer for ammonia synthesis catalysts for your company, please feel free to contact us.
SYAMCAT is a professional manufacturer of ammonia synthesis catalysts with over 30 years of catalyst experience and history. Through continuous technological innovation, we offer catalyst solutions for ammonia production. We are dedicated to assisting ammonia plants and fertilizer manufacturers in optimizing production efficiency while reducing environmental impact. Our aim is to contribute to the sustainability of global agriculture and food security.