Maximizing Ammonia Catalyst Efficiency: A SYAMCAT Guide for Emergency Handling and Operational Excellence
- Share
- Issue Time
- Dec 26,2023
Summary
Ammonia catalysts play a pivotal role in various industrial processes, particularly in ammonia plants, fertilizer factories, and engineering projects.
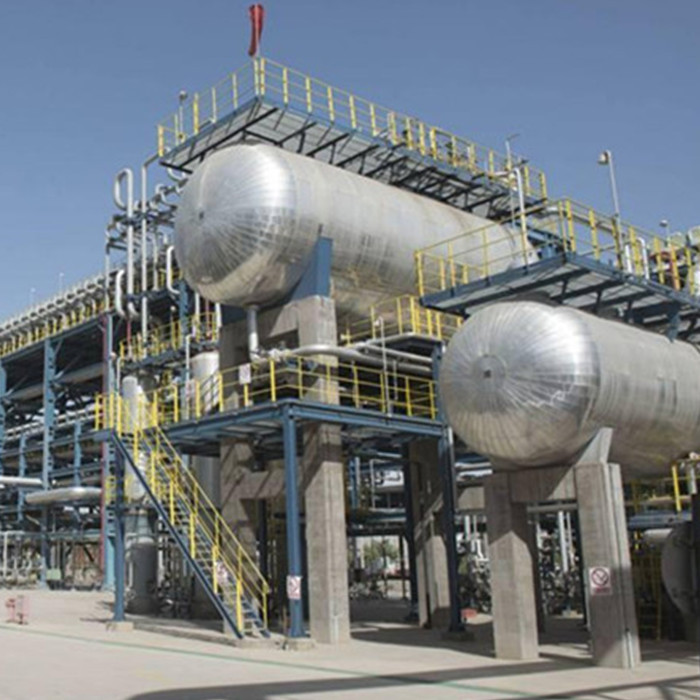
Maximizing Ammonia Catalyst Efficiency: A SYAMCAT Guide for Emergency Handling and Operational Excellence
Ammonia catalysts play a pivotal role in various industrial processes, particularly in ammonia plants, fertilizer factories, and engineering projects. The effective use and operation of these ammonia catalysts directly impact their performance and, consequently, the overall efficiency of production processes. In this comprehensive guide, we delve into SYAMCAT’s insights on emergency handling and operational best practices, addressing the critical aspects that operators and professionals in these industries should prioritize.
Sudden Power Outage
Emergency Shutdown for Asset Protection:
Immediately initiate a system shutdown to safeguard critical equipment, preserving valuable assets and preventing potential damage that could impact the long-term performance of ammonia catalysts.
Venting for Ammonia Catalyst Preservation:
After a power outage, especially during the crucial main water discharge phase, promptly vent the system to reduce water vapor content. This proactive step not only prevents ammonia synthesis catalyst damage but also ensures sustained efficiency, critical for maintaining optimal performance in ammonia plants and fertilizer factories.
Efficient System Replacement:
Execute a system replacement if necessary to further reduce water vapor content, ensuring the continued optimal performance of ammonia catalysts. This step minimizes potential disruptions and contributes to the long-term reliability of ammonia and fertilizer production processes.
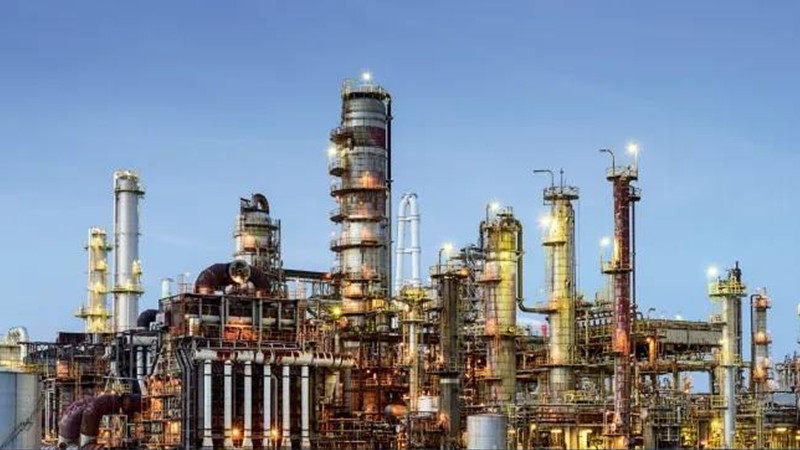
Caution in Pressure Release
Exercise caution during pressure release operations to prevent excessive pressure differentials inside and outside ammonia catalyst particles. This preventative measure minimizes the risk of catalyst breakage, ensuring the consistent and reliable performance of ammonia catalysts. Additionally, preventive actions against static electricity sparks and gas backflow enhance overall safety and contribute to prolonged ammonia catalyst service life.
Electric Furnace Malfunction
Minimizing Downtime for Continuous Production
In the event of an electric furnace malfunction, avoid an immediate shutdown. Prioritize a systematic approach to ensure low system water vapor, minimizing downtime and ensuring continuous production for ammonia plants, fertilizer factories, and related engineering firms.
Effective Fault Diagnosis
Thoroughly diagnose the specific cause of the electric furnace malfunction before stopping operations. This approach ensures more effective repairs, directly impacting operational efficiency across ammonia and fertilizer production processes and contributing to sustained catalyst performance.
Safety Assurance
Prioritize personnel safety during electric furnace repairs, strictly adhering to relevant safety procedures. This commitment ensures a secure working environment, benefiting the longevity of ammonia catalysts and the safety of personnel involved in ammonia plants, fertilizer factories, and engineering projects.
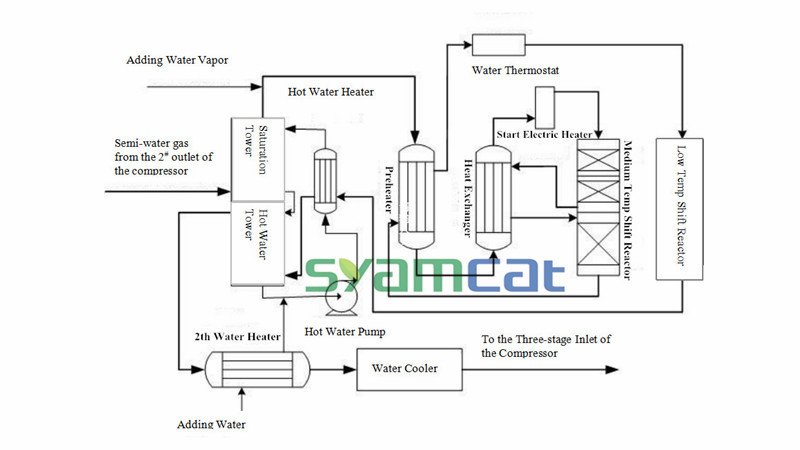
Poor Gas Quality
Dynamic Impurity Control for Catalyst Longevity
Respond dynamically to impurity increases in synthesis gas by adjusting operational parameters. This adaptive approach safeguards the catalyst, ensuring sustained efficiency and longevity, which are vital for meeting the rigorous demands of ammonia plants, fertilizer factories, and engineering projects.
Purification Process Verification
Investigate the gas purification process for quality issues, ensuring its normal operation to prevent trace impurities from entering the reduction system. This proactive verification contributes to consistent catalyst performance, meeting the stringent quality requirements of ammonia plants, fertilizer factories, and engineering firms.
Continuous Gas Composition Monitoring for Proactive Solutions
Regularly monitor gas composition to promptly detect and address any issues that may arise. This continuous monitoring ensures immediate corrective action, preserving the quality and efficiency of the ammonia catalyst, and meeting the diverse needs of ammonia plants, fertilizer factories, and engineering projects.
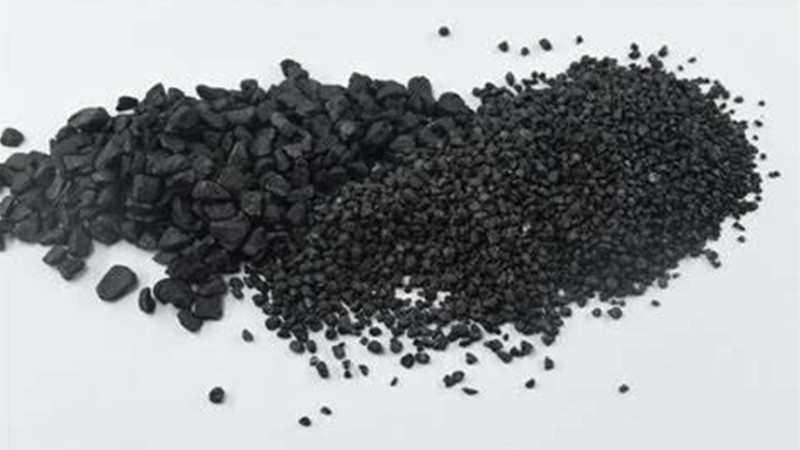
Tailored Solutions for Unique Scenarios
Preserving Operational Excellence
Implement specific measures for unique scenarios, such as copper washing processes, to prevent temperature anomalies during reduction. These tailored solutions address specialized challenges, ensuring the ammonia catalyst's optimal functioning and contributing to operational excellence across ammonia plants, fertilizer factories, and engineering projects.
In managing these operational aspects, operators in ammonia plants, fertilizer factories, and engineering firms benefit from SYAMCAT’s expertise, providing tailored insights and strategies. Extensive experience and adherence to operational procedures and safety standards are crucial for ensuring the safe and efficient operation of the catalyst and production equipment, ultimately maximizing the performance and service life of ammonia catalysts.
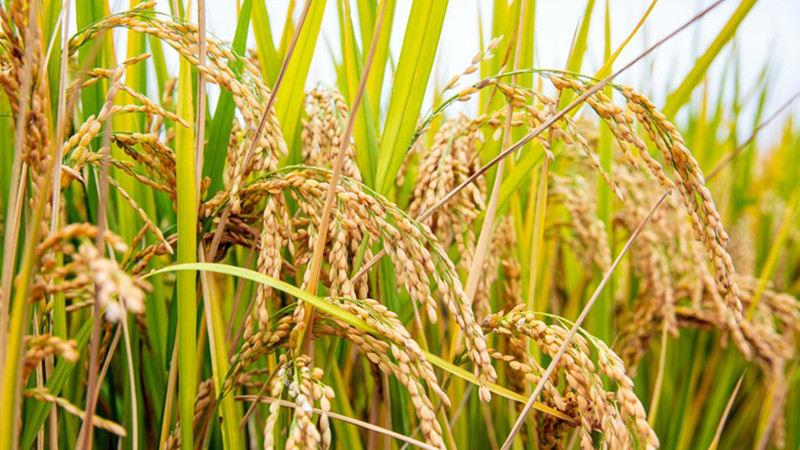
The above briefly introduces “Maximizing Ammonia Catalyst Efficiency: A SYAMCAT Guide for Emergency Handling and Operational Excellence” , If you would like to learn more or are in search of a manufacturer for ammonia synthesis catalysts for your company, please feel free to contact us.
SYAMCAT is a professional manufacturer of ammonia synthesis catalysts with over 30 years of catalyst experience and history. Through continuous technological innovation, we offer catalyst solutions for ammonia production. We are dedicated to assisting ammonia plants and fertilizer manufacturers in optimizing production efficiency while reducing environmental impact. Our aim is to contribute to the sustainability of global agriculture and food security.