Enhancing the Efficiency of Ammonia Synthesis Catalyst Reduction: A Customer-Focused Guide
- Share
- Issue Time
- Dec 20,2023
Summary
Understanding the complexities of ammonia synthesis catalyst reduction is vital for achieving optimal results.
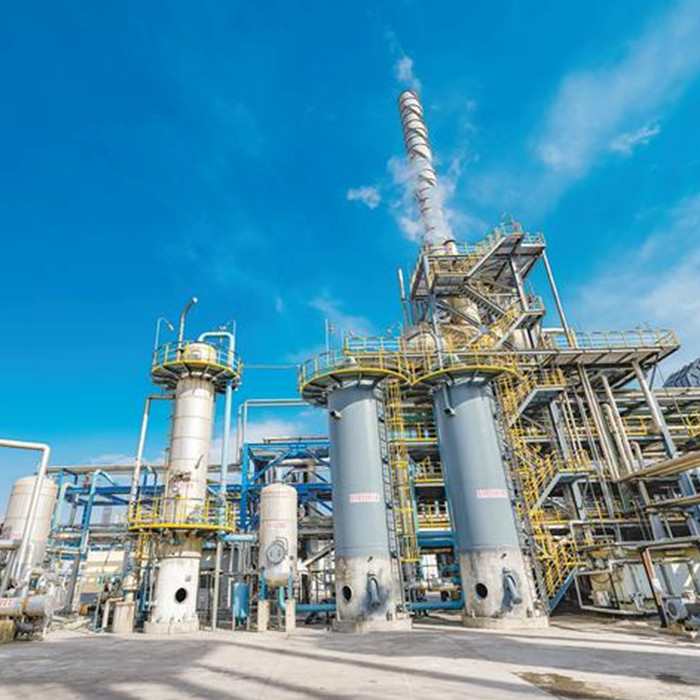
Enhancing the Efficiency of Ammonia Synthesis Catalyst Reduction: A Customer-Focused Guide
Understanding the complexities of ammonia synthesis catalyst reduction is vital for achieving optimal results. Here's a guide tailored to your needs:
Optimizing Reduction Temperature
Why it Matters: Controls efficiency and crystal grain growth.
Guidance: Gradually increase temperatures, with caution in main reduction. Implement isothermal reduction as needed to maintain water vapor concentration.
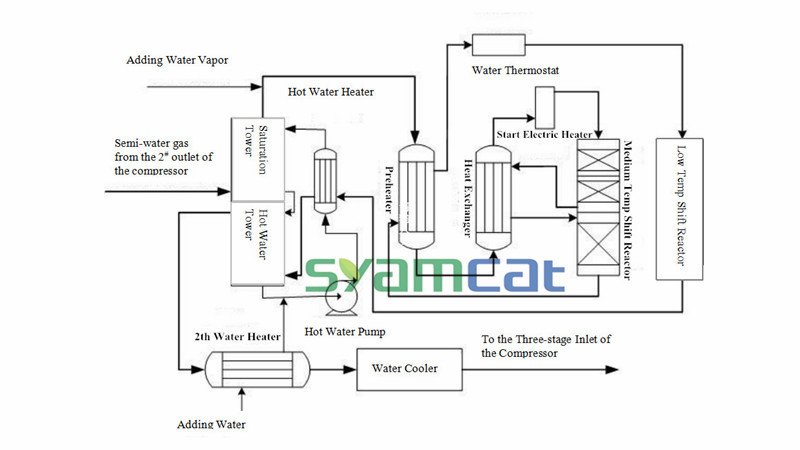
Managing Water Vapor Concentration
Significance: Essential for catalyst longevity.
Key Point: Efficient water vapor removal minimizes reoxidation, balancing low concentrations to avoid poisoning while ensuring a reasonable reduction time.
Enhancing Gas Velocity
Benefit: Increased velocity aids in reducing water vapor concentration.
Advice: Optimize gas velocity within furnace capacity and temperature requirements, starting lower and increasing gradually.
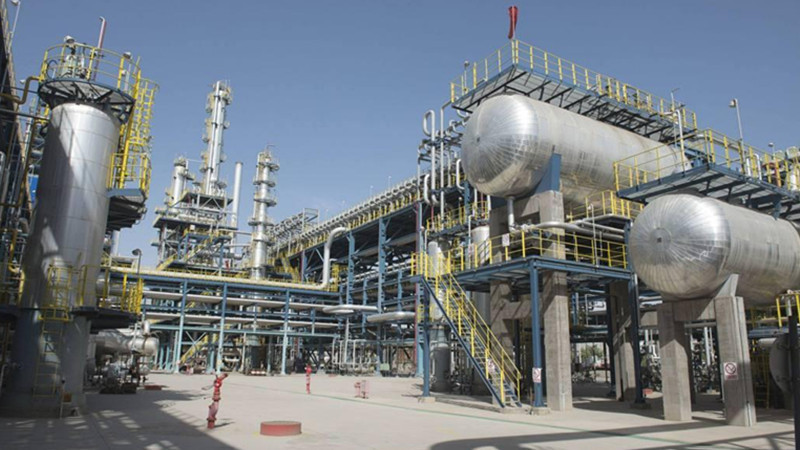
Pressure Considerations
Essential: Maintain lower pressures for thorough reduction.
Guideline: Differentiate pressure levels in various stages, ideally below 10 MPa during the main reduction, increasing toward the end.
Additional Factors for Optimal Performance
Ammonia in Reducing Gas: Inclusion prevents water freezing, ensuring uninterrupted reduction.
Recommendation: Suggest a balanced 3:1 hydrogen-to-nitrogen ratio during the main reduction phase for an efficient reaction and furnace startup assistance.
Oxygen-Containing Compounds: Control CO and CO2 for water-free hydrogenation.
Requirement: Stringently maintain total content below 30 ppm, ideally less than 10 ppm for modern chemical industry standards.
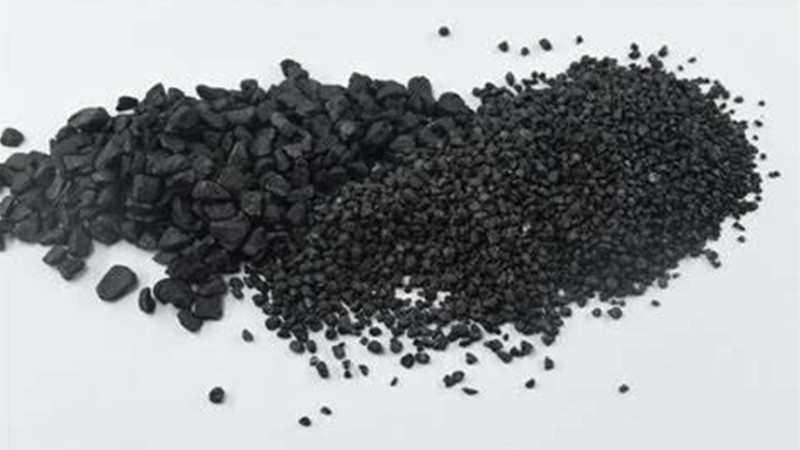
Customer Benefits
Enhanced Efficiency: Achieve optimal reduction results.
Extended Catalyst Life: Ensure longevity and sustained performance.
Smooth Operations: Avoid issues like crystal grain growth and reoxidation.
Improved Safety: Adherence to industry standards for a secure chemical environment.
In summary, following these guidelines ensures the efficient and effective reduction of synthetic ammonia catalysts, meeting your specific needs for optimal performance and longevity in industrial applications. Feel free to reach out for personalized assistance.
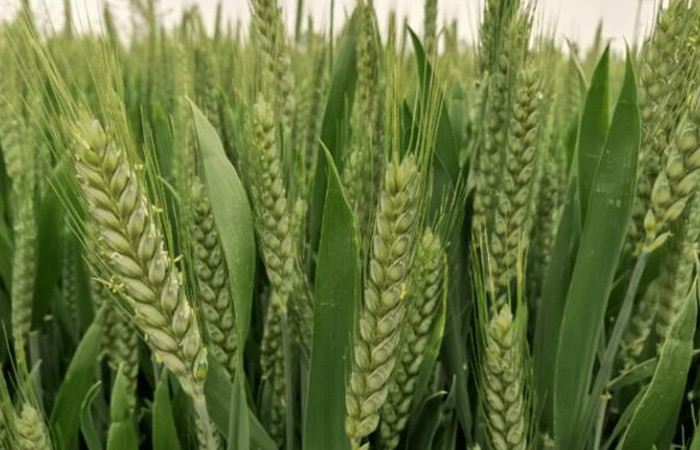
The above briefly introduces “Enhancing the Efficiency of Ammonia Synthesis Catalyst Reduction: A Customer-Focused Guide” , If you would like to learn more or are in search of a manufacturer for ammonia synthesis catalysts for your company, please feel free to contact us.
SYAMCAT is a professional manufacturer of ammonia synthesis catalysts with over 30 years of catalyst experience and history. Through continuous technological innovation, we offer catalyst solutions for ammonia production. We are dedicated to assisting ammonia plants and fertilizer manufacturers in optimizing production efficiency while reducing environmental impact. Our aim is to contribute to the sustainability of global agriculture and food security.