Optimizing Ammonia Synthesis: The Catalyst's Vital Role
- Share
- Issue Time
- Nov 15,2023
Summary
SYAMCAT's ammonia synthesis catalysts exhibit high catalytic features at low temperatures, excellent heat and poison resistance, and easy restoration characteristics.
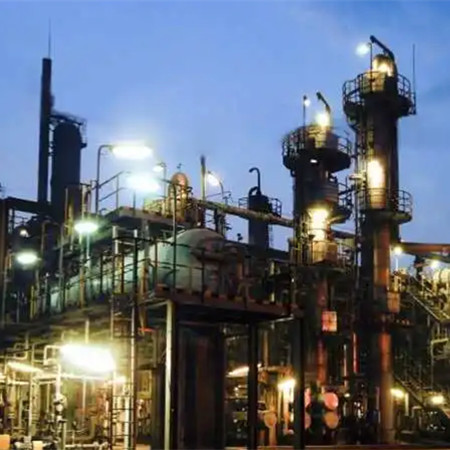
Optimizing Ammonia Synthesis: The Catalyst's Vital Role
Ammonia, denoted as NH3, undergoes direct synthesis from nitrogen and hydrogen, facilitated by high temperature, high pressure, and ammonia synthesis catalyst. Often referred to as ammonia gas, NH3 is primarily produced synthetically, with minimal recovery as a byproduct from coke oven gas.
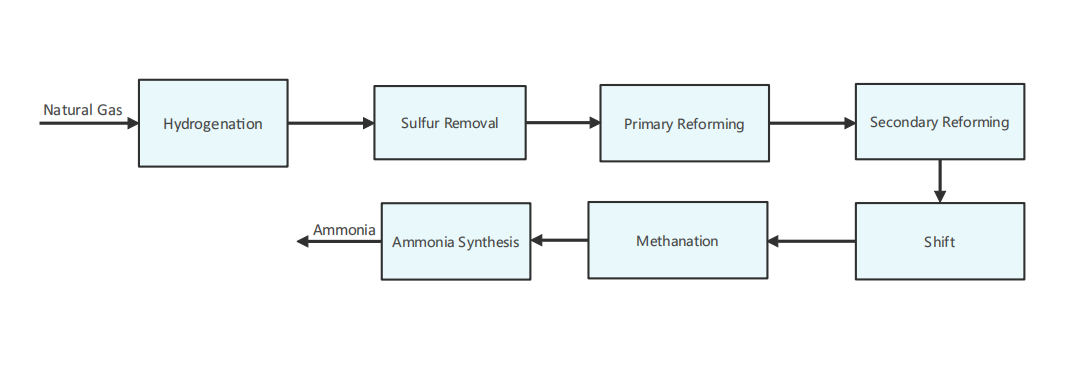
Key Production Methods of Ammonia
Natural Gas Synthesis:
Desulfurized natural gas undergoes secondary conversion, including carbon monoxide and dioxide removal, resulting in a nitrogen-hydrogen mixture.
Methanation removes residual carbon monoxide, yielding pure gas with a hydrogen-nitrogen molar ratio of 3, subsequently compressed for the ammonia synthesis loop.
Heavy Oil Synthesis:
Residue oil, inclusive of various deeply processed residues, contributes to synthesis gas production for ammonia through partial oxidation.
Simpler than natural gas steam conversion, this method requires an air separation unit for oxygen supply.
Coal (Coke) Synthesis:
As coal gains prominence in petrochemical and natural gas industries, it becomes a significant feedstock for ammonia production.
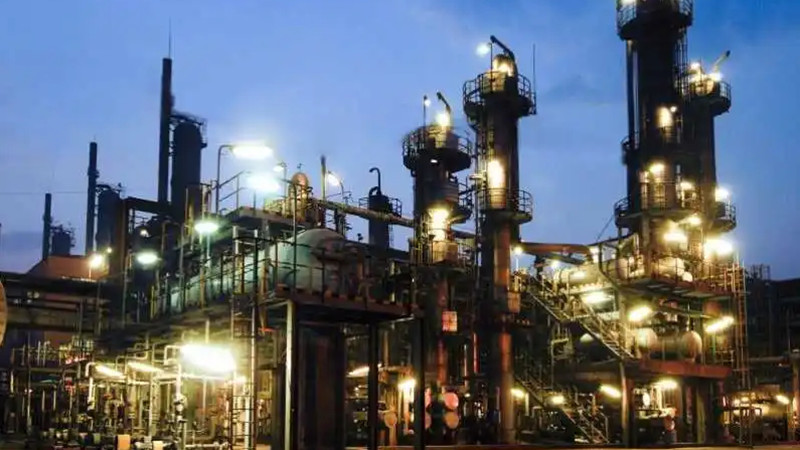
Versatile Ammonia Applications
Primary use in nitrogen and compound fertilizer manufacturing.
Serves as an industrial feedstock and ammonia-based livestock feed, comprising around 12% of global production.
Direct involvement in the production of nitric acid, nitrogen-containing inorganic salts, organic intermediates, sulfonamide drugs, polyurethane, polyimide fibers, and butadiene rubber.
Commonly utilized as a refrigerant in liquid form.
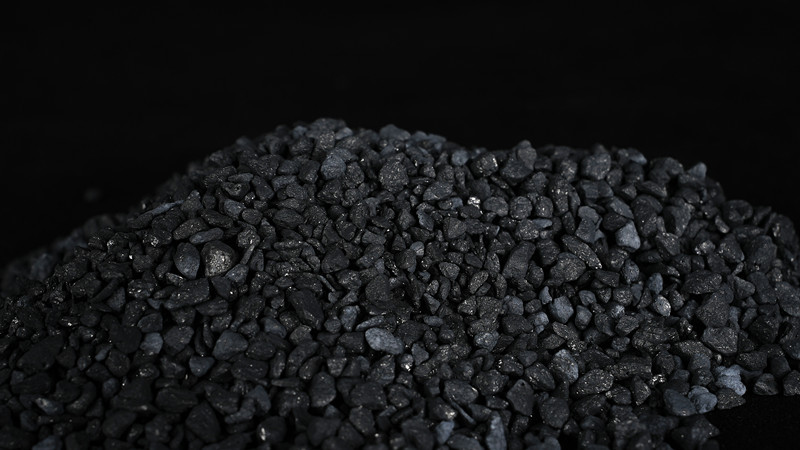
Catalytic Processes and Poisoning of Ammonia Synthesis Catalyst
Catalytic Processes of Ammonia Synthesis Catalyst:
Without a catalyst, ammonia synthesis demands a high activation energy of approximately 335 kJ/mol.
Introduction of iron-based catalysts divides the reaction into two stages with varying activation energies.
Catalysts undergo a maturation period, with activity gradually increasing to a standard level during their active service life.
Understanding Catalyst Poisoning:
Catalysts may experience poisoning during their stable period, significantly reducing or destroying activity.
Poisoning is categorized as temporary or permanent, with temporary poisoning reversible using pure hydrogen-nitrogen gas.
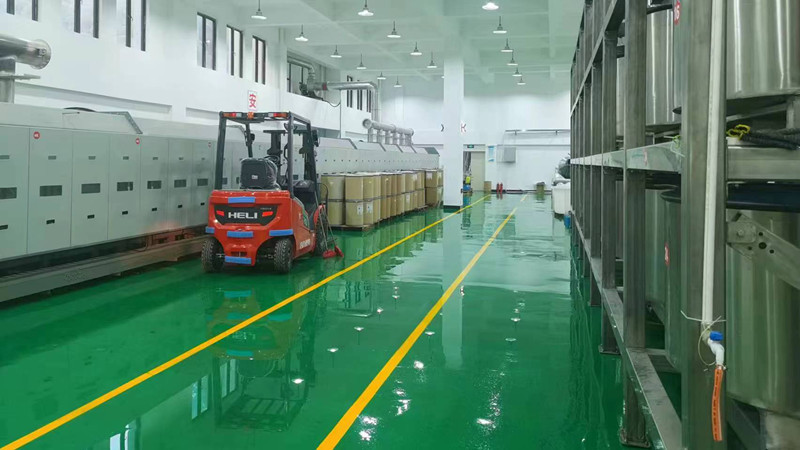
SYAMCAT's ammonia catalysts exhibit high catalytic features at low temperatures, excellent heat and poison resistance, and easy restoration characteristics.
Explore SYAMCAT's Catalyst Solutions:
If you seek a reliable manufacturer for ammonia synthesis catalysts, SYAMCAT offers over 30 years of catalyst expertise. With a focus on technological innovation, we provide solutions for optimizing ammonia production. Our commitment is to assist ammonia plants and fertilizer manufacturers in enhancing production efficiency while minimizing environmental impact. Contact us for more information and discover how SYAMCAT contributes to the sustainable development of global agriculture and food security.