The Impact of Active Components on Ammonia Synthesis Catalysts
- Share
- Issue Time
- Nov 2,2023
Summary
It is a catalyst with dual active components, iron, and cobalt. During the melting process, cobalt oxide reacts with magnetite, forming a eutectic mixture.
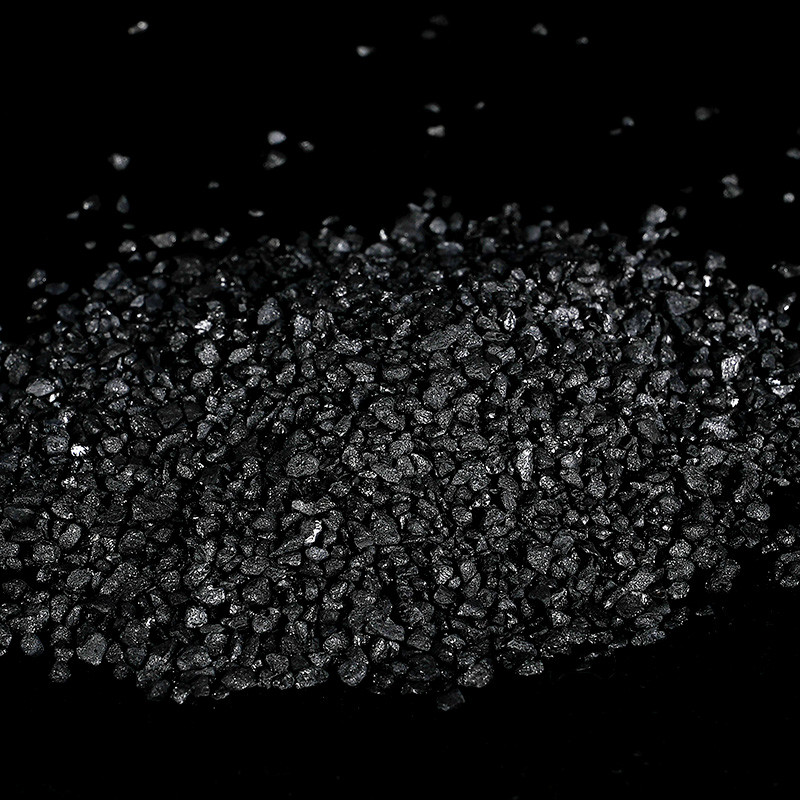
The Impact of Active Components on Ammonia Synthesis Catalysts
The synthesis of ammonia has undergone a long journey spanning over a century. During this period, researchers have tirelessly explored methods to reduce energy consumption and maximize ammonia capacity. The challenge lies in finding a balance between increasing capacity and minimizing the energy input for ammonia and fertilizer plants.
In the history of ammonia synthesis, it's well-known that the equilibrium state of the reaction, as represented by the equation:
N+3H2NHH=-91.4KJ/mol
Experimental evidence has shown that without catalysts, it takes an impractically long time for the reaction to reach equilibrium. In fact, under these conditions, achieving ammonia synthesis at an industrial scale is fundamentally impossible.
Therefore, finding and developing novel ammonia synthesis catalysts and applying them in industrial production are crucial for increasing ammonia production. However, the efficiency of catalysts is significantly influenced by their active components. These active components act as the driving force behind chemical reactions, serving as the heart of the catalysts, determining the reaction rates and efficiency. In ammonia synthesis, these active components play a pivotal role in determining the catalyst's performance.
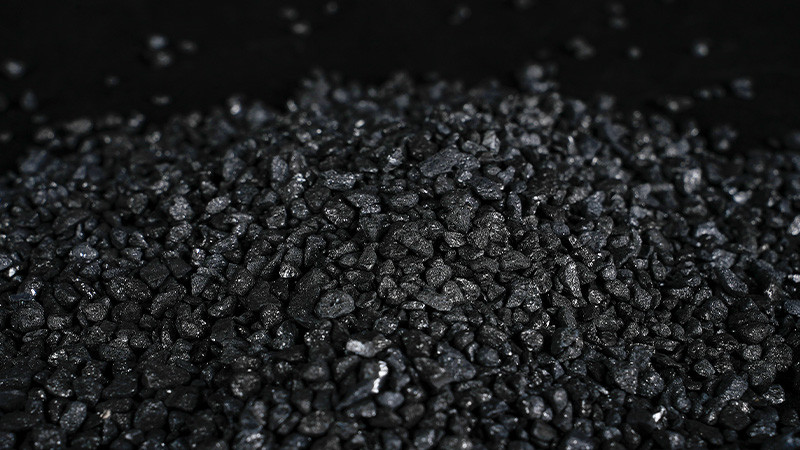
In industrial applications, ammonia synthesis catalysts are required to have not only low-temperature high activity but also long service life, excellent resistance to poisoning, affordability, and easy accessibility. These criteria ensure that the catalysts are not only efficient but also practical and economically viable for large-scale production.
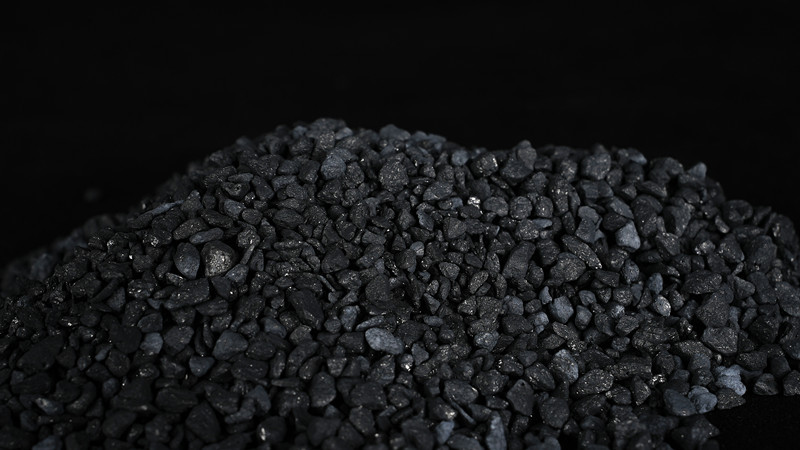
The main component of the SYAMCAT A217 ammonia synthesis catalyst is iron(III) oxide (Fe2O3), and it contains appropriate amounts of cobalt oxide (Co3O4), aluminum oxide (Al2O3), potassium oxide (K2O), calcium oxide (CaO), and other additives. The SYAMCAT A217R ammonia synthesis catalyst is derived from the SYAMCAT A217 catalyst through a pre-reduction process conducted in specialized factory equipment. In order to ensure safety during transportation, storage, and loading processes, controlled passivation is applied to the surface of the catalyst particles, including the micro-porous surface. Oxygen is used to form a controlled FeO film on the surface, ensuring the catalyst's safety and easy reducibility during use. After pre-reduction, the SYAMCAT A217R ammonia synthesis catalyst achieves a reduction degree of over 90%, and its oxygen content is generally below 2%.
he above briefly introduces “The Impact of Active Components on Ammonia Synthesis Catalysts”, If you would like to learn more or are in search of a manufacturer for ammonia synthesis catalysts for your company, please feel free to contact us.
SYAMCAT is a professional manufacturer of ammonia synthesis catalysts with over 30 years of catalyst experience and history. Through continuous technological innovation, we offer catalyst solutions for ammonia production. We are dedicated to assisting ammonia plants and fertilizer manufacturers in optimizing production efficiency while reducing environmental impact. Our aim is to contribute to the sustainable development of global agriculture and food security.