What factors should be considered when selecting a steam reforming catalyst?
- Share
- Issue Time
- Feb 19,2024
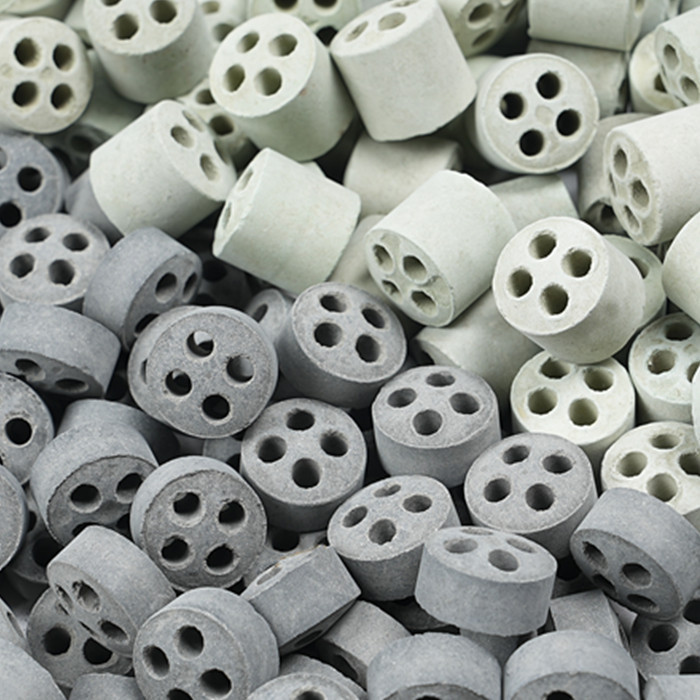
What factors should be considered when selecting a steam reforming catalyst?
When selecting a steam reforming catalyst, several factors should be considered, including:
Catalyst Composition: The catalyst's composition, often based on nickel, is crucial for its performance in steam reforming reactions.
Activity and Stability: The catalyst's ability to maintain high activity over time without significant degradation is essential for efficient and continuous operation.
Resistance to Deactivation: Catalysts should resist deactivation due to factors like carbon deposition, sulfur poisoning, and other contaminants in the feedstock.
High Surface Area: A catalyst with a high surface area provides more active sites for reactions, contributing to improved efficiency.
Temperature Range: Consideration of the temperature range in which the catalyst operates optimally is crucial for the overall efficiency of the reforming process.
Specific Reaction Requirements: Different catalysts may be better suited for specific reactions or feedstock compositions, so matching catalyst characteristics to process requirements is vital.
Catalyst Life and Regeneration: The ability to regenerate or replace the catalyst efficiently impacts the overall lifecycle cost and sustainability of the process.
Cost: Cost considerations, including the initial investment and maintenance costs, play a significant role in the selection of a steam reforming catalyst.
Safety and Environmental Impact: Ensuring that the catalyst aligns with safety standards and has minimal environmental impact is increasingly important in the selection process.
Manufacturer Reputation: Choosing a catalyst from a reputable manufacturer with a history of producing reliable and high-performance catalysts can be a key factor in decision-making.
By carefully evaluating these factors, industries can make informed decisions in selecting steam reforming catalysts that best suit their specific requirements and operational conditions.